Developing Safe Rechargeable Batteries
Background
Since its commercialization in 1991, Li-ion batteries (LIB) became an indispensable power source in our daily life activities. We use them in our mobile phones, laptops, electric vehicles, and many more mobile applications. As shown in the Ragone plot (middle figure), lithium-based batteries have the highest gravimetric and volumetric specific energy and power densities among the other commercialized batteries technology. However, this great technology faces two major challenges, namely: the limited energy density (despite its superiority over the other battery technologies) and the low safety of the batteries. Both challenges can be better grasped after the working principle of LIBs is explained (see right-most figure).
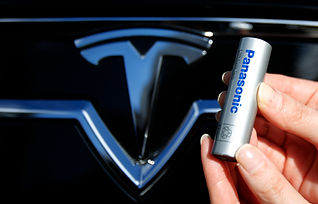
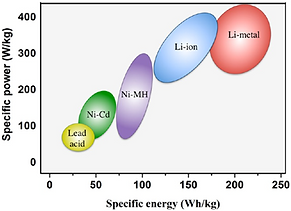

LIBs consist of three main components. A negative electrode (anode), a positive electrode (cathode), and an electrolyte. During discharge and charge, Li-ions (Li+) transport from the anode to the cathode, and vice versa, through the ion-conducting electrolyte. Both electrodes have a concentration of host sites (in an intercalation-type electrodes) where Li+ can be stored and taken out, via an intercalation and deintercalation reactions, respectively. The concentration of host sites in the electrode reflects its specific capacity (mAh/g). The electrode’s voltage is related to the thermodynamics of the (de)intercalation reactions as expressed in:

where the numerator is the Gibbs free energy of the (de)intercalation reaction, n is the number of electrons transferred, and F is the Faraday’s constant.
The specific energy density = specific capacity x voltage. Thus, increasing the energy density of LIBs can be achieved by increasing the specific capacity of the cathode or the battery voltage, or both together. The challenge associated with the use of high voltage cathode is the availability of a suitable electrolyte. For instance, the electrolyte should have a sufficiently wide electrochemical window so that the battery can operate at such high voltages, otherwise, the electrolyte would decompose.
Another approach to increase the energy density of LIBs is to replace graphite (specific capacity~370 mAh g-1), which is the commercially used anode, by the lithium metal (specific capacity~3800 mAh/g). Therefore, given a specific volume constraints of a battery pack, one can pack hundreds of more batteries if lithium metal (LM) is used instead of graphite. However, this approach is also challenged by the availability of a suitable electrolyte that is compatible with LM. One of the critical compatibility issues between LM and battery electrolytes is the initiation and growth of Li dendrites. During the cycling of a lithium metal battery (LMB), the LM experiences volumetric changes and lithium dendrites may grow out of the LM surface. If dendrites reach the positive electrode, it will short circuit the battery, causing a significant safety risk.
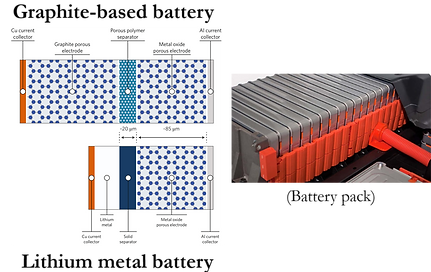
Therefore, electrolytes not only have a significant role in increasing the energy density of LIBs, but also in enhancing their safety. The electrolytes commercially used in LIB are highly flammable. If the battery is overheated, it can easily ignite and experience a thermal runaway. If we can use less-flammable (or ultimately non-flammable) electrolytes, that also have sufficiently wide electrchemical window and are compatible with LM, not only we can alleviate the safety hazards of LIB, but we also can increase the energy density of the batteries.
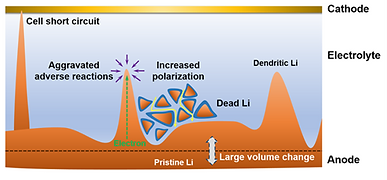
Electrolytes are a central component in the battery cells. It is where Li-ions get transported between the two battery electrodes (anode and cathode). A good electrolyte should have several properties that include: high ionic conductivity, high chemical compatibility with all battery cell components, wide electrochemical window, good wetting properties, high thermal stability, low (or zero) flammability, low viscosity and/or good mechanical contact with battery electrodes. Developing an electrolyte that achieves all such requirements is a real challenge. Although the commercial carbonate-based electrolytes are characterized by their high ionic conductivity, their flammability issues necessitated the search for alternative non/less flammable electrolytes. The search space for such alternative electrolytes is vast, as it spans the entire broad fields of organic and inorganic chemistry. For instance: inorganic ceramic electrolytes, (composite) polymer electrolytes, ionic-liquids, plastic-crystals, sulfones, phosphorus-based solvents, are all suggested.
The successful making an alternative electrolyte is a non-trivial process, as it requires an experience for deciding the composition of the electrolyte and the synthesis/processing scheme. When a candidate electrolyte is prepared, it is then subjected to an extensive investigations on its physical and electrochemical properties, using the appropriate techniques.
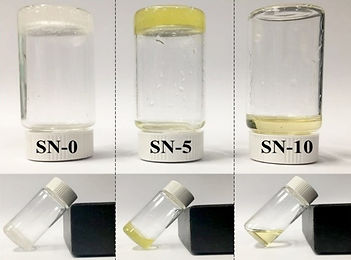

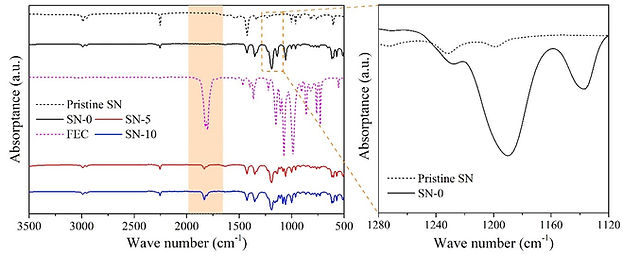

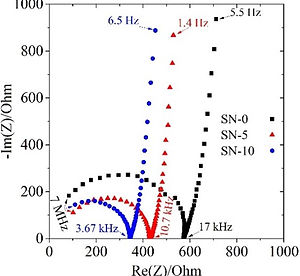

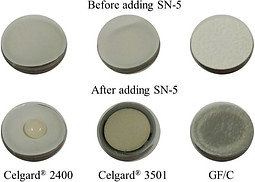
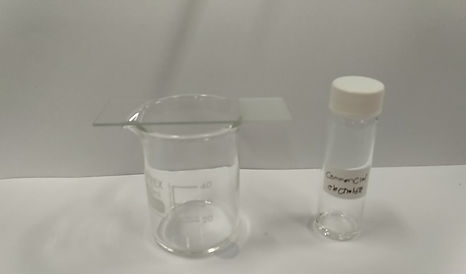
Burning test for commercial battery electrolyte
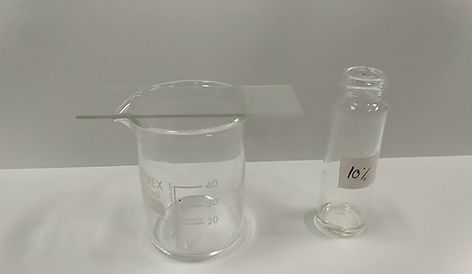
Burning test for a developed alternative battery electrolyte
After the electrolyte passes the basis characterization tests, we begin to study the performance of the electrolyte when cycled with battery electrodes in a symmetric, half, and full cell configurations. After finishing such tests, it is very beneficial to perform a post-mortem analysis on the cycled batteries to grasp the reasons for any under-performance of the batteries, and to draw conclusions on how to extend the batteries' cycle life.
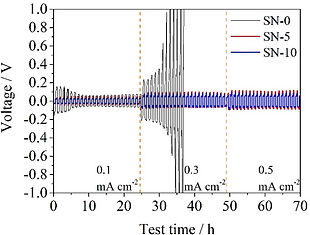

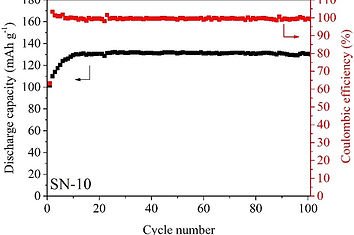
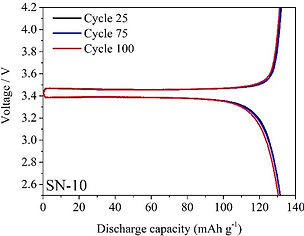

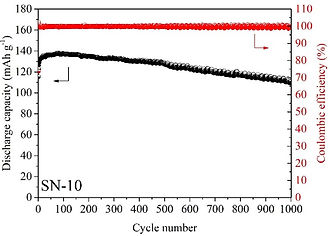
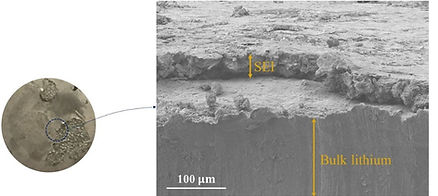
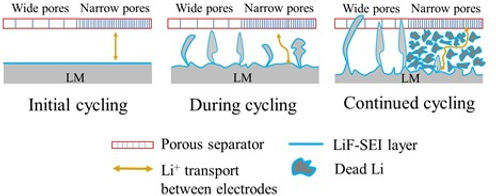
Selected Publications:
[1] Effat, M.B., Lu, Z., Belotti, A., Yu, J., Lyu, Y.Q. and Ciucci, F., 2019. Towards succinonitrile-based lithium metal batteries with long cycle life: The influence of fluoroethylene carbonate loading and the separator. Journal of Power Sources, 436, p.226802. [link]
[2] Lu, Z., Yu, J., Wu, J., Effat, M.B., Kwok, S.C., Lyu, Y., Yuen, M.M. and Ciucci, F., 2019. Enabling room-temperature solid-state lithium-metal batteries with fluoroethylene carbonate-modified plastic crystal interlayers. Energy Storage Materials, 18, pp.311-319. [link]
[3] Yu, J., Kwok, S.C., Lu, Z., Effat, M.B., Lyu, Y.Q., Yuen, M.M. and Ciucci, F., 2018. A ceramic‐PVDF composite membrane with modified interfaces as an ion‐conducting electrolyte for solid‐state lithium‐ion batteries operating at room temperature. ChemElectroChem, 5(19), pp.2873-2881. [link]
To avoid the problem of lithium dendrites, which may occur when battery cells operates at high power, anodes alternative to graphite or lithium metal are needed. In this regard, LTO is good alternative as it has zero strain, etc. However, as voltage of LTO is 1.5 vs. Li+/Li (compared to 0 V vs. Li+/Li for LM), the energy density of battery cell would be scarified except when high voltage cathode is used. Here, comes the NxMyCz family (layered oxide materials composed of Nickel, Manganese, and Cobalt) as promising cathodes. By tuning the x,y,z of NMC, several types of NMC can be made. The higher the Ni content the higher is the capacity, but also the lower is the safety of the battery. Consequently, it is paramount to use safe quasi solid-state electrolyte (QSSE). When such an LTO/QSSE/NMC battery is to be developed, significant engineering is needed. For instance, we need to ensure that all Li inside the cell will be cyclable for longest possible period, without undergoing side reactions with any of the cell components. When such batteries are engineered for application as electric vehicles, the battery must preserve such good performance in a wide range of temperatures, spanning subzero to above room temperature.
The making of such batteries is indeed challenging, but also very interesting!

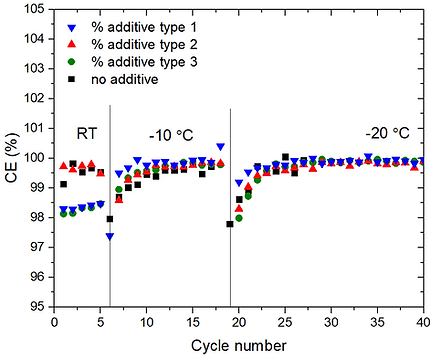
Selected Publications:
[1] Effat, M.B., Kwok, S.C., and Ciucci, F., 2020. Unpublished technical report.
[2] Lin, X., Zhou, G., Liu, J., Yu, J., Effat, M.B., Wu, J. and Ciucci, F., 2020. Rechargeable Battery Electrolytes Capable of Operating over Wide Temperature Windows and Delivering High Safety. Advanced Energy Materials, 10(43), p.2001235. [link]